products
permanent magnets & assemblies
PERMANENT MAGNETS
Allstar Magnetics provides a range of permanent magnetic materials, suitable for a multitude of costs, applications, and working environments. We offer highly distributed commercial solutions, as well as unique rare earth materials. View the information below for an overview of properties by magnetic energy, heat resistance, and composition and/or grade. Please contact a team member to source the right material for your project.
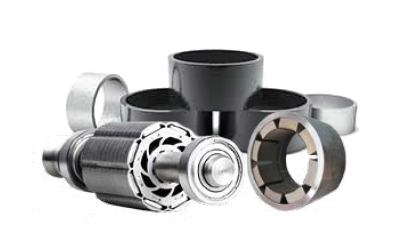
PERMANENT MAGNETIC ASSEMBLY
Precise technical, operational, and production capabilities, focused on the most cost-effective manufacturing process. We work with you from design conception & development to final product shipment. Streamline your supply chain with turnkey magnetic assemblies tailored to your project needs.
We understand the unique applications of permanent magnetic materials. Streamline your supply chain with assembled solutions tailored to your project needs. Our team are experts in problem-solving magnetic applications for a variety of industries, with services in design, testing, and engineering.
Neodymium
Properties
Neodymium iron boron magnets are widely used today and have two basic types; sintered and bonded (See Bonded Magnets Section). Within those two types, there are numerous different grades with distinctly different properties. Sintered neodymium iron boron magnets are also known as Nd2Fe14B magnets, neodymium magnets, neo magnets, Nd-Fe-B magnets, or 2:14:1 magnets. Sintered Nd2Fe14B has a tetragonal crystal structure. The materials were developed in the 1980’s and both sintered and bonded magnets are surrounded by several patents. It is important to verify that the supply chain is a licensed producer for any neo magnets.
The heavy rare earth element, Dysprosium, is often added to increase intrinsic coercivity and maximum operating temperature. Small amounts of other transition metals, such as Al, Co, Cu, Nb and/or Ga, can be added to modify the microstructure to improve performance.
Nd2Fe14B has the highest room temperature maximum energy product, (BH)max, up to 52 MGOe. They are generally less expensive than SmCo and Alnico. Mechanically they are less brittle than SmCo but require a surface coating to protect from corrosion. Ni plating, epoxy coating, aluminum ion vapor deposition (IVD) and parylene are some of the common types of surface treatment for Nd-Fe-B magnets.
The relatively low Curie temperature (310-400 oC) compared to SmCo (700-820 oC) and Alnico (700-860 oC ) give them a lower maximum operating temperature. The operating temperature must be considered when selecting a grade of material. It is critical to validate that the Nd-Fe-B magnetic working point is well above the knee on the demagnetization curve to avoid demagnetization of the magnet at elevated temperatures.
Samarium Cobalt
Properties
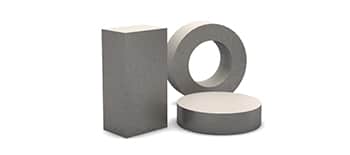
There are two families of Sm-Co magnets — SmCo5 and Sm2Co17. SmCo5 was developed in the 1960s and further development produced Sm2Co17 in the 1970s.
SmCo5 has a hexagonal crystal structure that consists of five atoms of cobalt for each samarium atom. SmCo5 magnets are also known as Sm-Co 1:5, samarium-cobalt 1:5 magnets, SmCo series 1:5 magnets, or sometimes as 1:5 magnets.
Sm2Co17 has a rhombohedral crystal structure, which is obtained by replacing Sm atoms in the SmCo5 hexagonal structure with a pair of Co atoms. Other elements are added to improve properties such as intrinsic coercivity or reversible temperature coefficient. Elements such as iron, copper, hafnium, gadolinium, terbium, erbium and zirconium are commonly used. Sm2Co17 is also known as samarium-cobalt 2:17, SmCo Series 2:17, Sm(Co,Fe,Cu,Zr)z or sometimes as 2:17 magnets.
1:5 has a maximum energy product, (BH)max, around 20 MGOe. The reversible temperature coefficient of residual induction of SmCo5 is about -0.04%/°C. 2:17 has a maximum energy product (BH)max as high as 35 MGOe. The reversible temperature coefficient of residual induction is about -0.035%/oC.
Both SmCo5 and Sm2Co17 have very high intrinsic coercivity, Hci, a measurement of resistance to demagnetization. They also have very good corrosion resistance, thermal stability and resistance to radiation. Although brittle, they do not require a surface coating and can be used at temperatures up to 300oC.
The relatively low Curie temperature (310-400 oC) compared to SmCo (700-820 oC) and Alnico (700-860 oC ) give them a lower maximum operating temperature. The operating temperature must be considered when selecting a grade of material. It is critical to validate that the Nd-Fe-B magnetic working point is well above the knee on the demagnetization curve to avoid demagnetization of the magnet at elevated temperatures.
Alnico
ALNICO (Al-Ni-Co) HAS THE HIGHEST TEMPERATURE THRESHOLDS OF ALL PERMANENT MAGNETIC MATERIALS, AND IS A STRONG, STABLE PERMANENT MAGNET WITH ELECTRICALLY CONDUCTIVE PROPERTIES. IT FEATURES SEVERAL GRADES WITH DIFFERENT MAGNETIC CHARACTERISTICS.
Properties
Alnico is an acronym for a family of iron-based magnet alloys, which also contain aluminum (Al), nickel (Ni), cobalt (Co), hence, al-ni-co. The magnets also contain copper (Cu) and, sometimes, titanium (Ti). A typical Alnico magnet contains 7–12% Al, 14–25% Ni, 5–38% Co, 3-4% Cu, with the balance being Fe.
Alnico magnets have very high Curie temperature (about 800 °C) and offer very good thermal stability up to temperatures as high as 540 °C. Alnico is brittle and electrically conductive. Its residual induction (Br) is very high (up to 13.5 kG), but the intrinsic coercivity (Hci) is very low (typically from 550 to 2000 Oersteds), therefore Alnico magnets can be easily demagnetized by external demagnetizing fields.
The low intrinsic coercivity of Alnico magnets can also be used as an advantage because magnets can also be easily tuned or adjusted in an assembly. Although other rare earth magnets have become more popular due to their high magnetic flux density and high intrinsic coercivity, Alnico magnets continue to be selected for certain magnetic systems and exceptionally high-temperature applications.
Both SmCo5 and Sm2Co17 have very high intrinsic coercivity, Hci, a measurement of resistance to demagnetization. They also have very good corrosion resistance, thermal stability and resistance to radiation. Although brittle, they do not require a surface coating and can be used at temperatures up to 300oC.
The relatively low Curie temperature (310-400 oC) compared to SmCo (700-820 oC) and Alnico (700-860 oC ) give them a lower maximum operating temperature. The operating temperature must be considered when selecting a grade of material. It is critical to validate that the Nd-Fe-B magnetic working point is well above the knee on the demagnetization curve to avoid demagnetization of the magnet at elevated temperatures.
Ceramic
Properties
Ceramic magnets are also known as hard ferrites or ferrite magnets, which are composed of primarily iron oxide (Fe2O3). The two common compositions are: strontium ferrite, SrFe12O19 (SrO·6Fe2O3) and barium ferrite BaFe12O19 (BaO·6Fe2O3). Soft ferrites have lower coercivity and the common compositions are manganese-zinc ferrite (MnZn, with the formula MnaZn(1-a)Fe2O4) and nickel-zinc ferrite (NiZn, with the formula NiaZn(1-a)Fe2O4).
Ceramic magnets can be either isotropic or anisotropic. Isotropic ceramic magnets can be magnetized in any direction while the anisotropic ceramic magnets can only be magnetized through the easy axis (magnetization direction). They have very high electrical resistivity (around 106 Ohm-cm) and positive reversible temperature coefficient of intrinsic coercivity.
Ceramic maximum energy product, (BH)max, is lower than other permanent magnets, so they are typically much larger magnets in actual application. By weight, they are the most widely used magnet globally. Ceramics are chemically stable and the least expensive magnets due to inexpensive raw materials and processes. Maximum energy product, (BH)max, of 1 to 4 MGOe, is lower than that of rare earth magnets but intrinsic coercivity, Hci, from 2500 to 4000 Oersteds, (higher than Alnico). Ceramic magnets are a cost-effective choice in many industrial applications.
Bonded
Properties
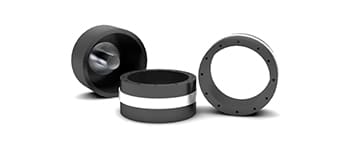
Bonded magnets are a class of products that are made by combining the microcrystalline form of rare earths with a polymer or other binders. Typically, most bonded magnets use NdFeB powders, but some high temperate applications use SmCo or Alnico powders. The binders are generally non-magnetic and can be either a thermoplastic or elastomeric binder.
Processing for bonded magnet vary and can include extrusion, injection molding, compression bonding and calendaring depending on the end application. The trade off with adding the binder is a lower energy product but significantly improved mechanical properties. Bonded magnets can be formed into small or complex geometries with extreme accuracy on tolerances and no secondary finishing operations. These types of production methods are most cost-effective with high volume applications.
The microcrystals are uniformly distributed in all orientations, so there are equal magnetic properties in all directions, which is why bonded magnets are considered isotropic. This allows them to be magnetized in any direction and a common application are multipole devices. Multipole magnets are magnetized to have many alternating poles which cannot be achieved in convention sintered magnets. Multipole rings with 100+ poles are typical for sensor applications.
Radial Ring
Properties
Bonded magnets are a class of products that are made by combining the microcrystalline Radial magnets are a unique sub-set of a NdFeB sintered magnets. Using proprietary technologies, a multipole ring can be sintering into a single geometry. This replaces the costly and labor-intensive method of gluing arc, bread loaf or rectangle segments on to a rotor shaft.
Allstar Magnetics now offers high-efficiency multipole Neodymium (NdFeB) magnetic rings. These rings are revolutionizing the permanent magnet space for synchronous motors, stepping motors and DC brushless motors widely used in automotive, specialty electronics, and medical applications.
Magnets are pressed to produce sintered NdFeB magnets. This process consists of combining base powders, pressing the resulting material, and then baking or sintering the resulting ring to achieve a radially magnetized product.
This new technology improves the uniformity of magnetic flux for increased motor efficiency and torque. Other benefits include ease of assembly, superior mechanical properties and eliminates the re-work associated with chipped discrete magnets.