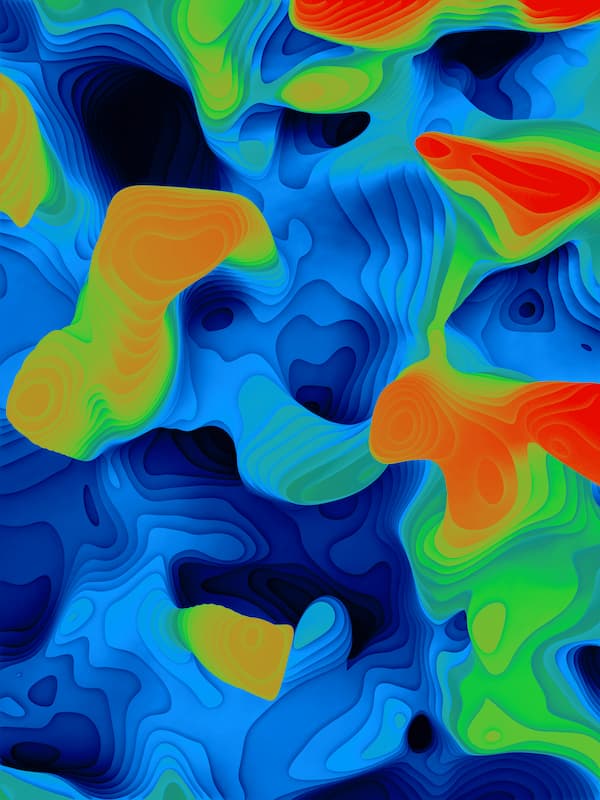
Project Overview: The client required a complex milled ferrite and wound wire set for their LiDAR application, designed to allow data and power to move independently without interference. While theoretically feasible at the prototype level, no attempt at volume manufacturing had succeeded due to material and winding complexities. Prior efforts had failed, resulting in critical delays for the client’s product development. Allstar Magnetics partnered with the client to overcome these challenges, leveraging their expertise in CNC milling, winding, and material development to deliver an innovative solution.
Allstar’s Approach: Allstar Magnetics devised a comprehensive manufacturing process to address the project’s unique demands. From optimizing CNC milling parameters to developing a robust winding and gluing process, the team ensured that all components met stringent performance specifications. A 24/5 production strategy enabled consistent high-volume output, while innovative packaging solutions facilitated seamless assembly for the client’s end-use.
Client Testimonial: “Allstar Magnetics’ ability to combine material expertise with advanced CNC milling and winding techniques was the key to overcoming the challenges we faced. Their innovative approach and commitment to quality allowed us to move from prototypes to full-scale production, exceeding our expectations and enabling the success of our LiDAR program.”
Conclusion: Comprehensive magnetic solutions, all in one place. Allstarmagnetics.com Through a combination of CNC milling, material expertise, and precision manufacturing techniques, Allstar Magnetics enabled the client to achieve what had previously been impossible: high-volume production of a complex milled ferrite and wound wire set. This case study underscores the value of Allstar’s holistic approach to solving intricate manufacturing challenges, positioning their client for long-term success in the rapidly evolving LiDAR technology sector.
Key Aspects of the Project:
- Research & Material Development: Allstar conducted extensive research to understand the materials’ specific properties and challenges, laying the groundwork for a reliable manufacturing process.
- CNC Milling: The team established optimal cutting tools and RPM levels to precisely mill the specialty ferrite components, implementing high-efficiency placement arrays for volume production.
- Prototype Conversion to Volume Production: What began as a prototype was rapidly scaled into a repeatable, high-volume manufacturing process.
- Winding and Gluing: A refined winding and gluing process minimized breakage and maintained precise inductance specifications.
- Testing: 100% AQL testing ensured compliance and reliability, with all data communicated to the client in advance.
- Packaging: Allstar designed new packaging materials and layouts to ensure safe transportation and immediate usability upon delivery.
Results: Allstar Magnetics delivered a manufacturing solution that allowed the client to:
- Ramp up production 10x within 30 days.
- Eliminate nearly all in field failures associated with the milled and wound components.
- Secure larger contracts and advance their program from concept to growth phase.
- Achieve exceptional reliability and durability in the critical ferrite and winding components, ensuring the success of their LiDAR product.
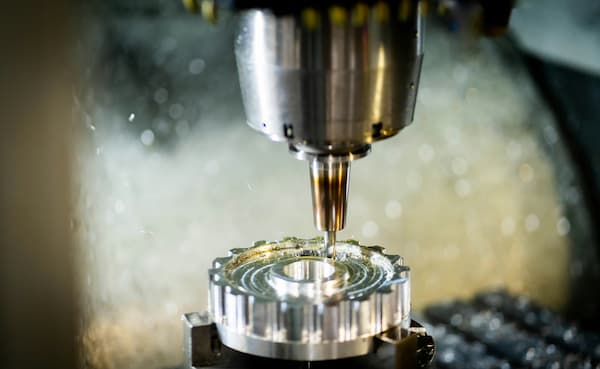